Quality Control
Rich experience
- As a factory that has been deeply engaged in the production of hydraulic vibratory hammers for 39 years, we boast a 200,000-square-meter production base and a workforce of 500 employees. We are equipped with various professional finishing equipment, including five-axis gantry milling machines imported from Germany, enable us to achieve high-precision processing during the product manufacturing process. This ensures that the parts of our hydraulic vibratory hammers are processed with a fineness reaching the top level in the industry, thereby enhancing the overall performance and quality reliability of our products. Our long-term industry presence has endowed us with profound technical expertise and rich production experience. This enables us to quickly respond to market demands, solve various technical problems, and continuously introduce high-quality hydraulic vibratory hammer products that meet the diverse needs of customers and lead the market.
Innovation
- Variable moment technology:
This technology allows driving with adjustable amplitude thanks to the variation of the eccentric’s relative positions.
VM series variable moment hydraulic vibratory hammers ensure maximum performance for minimum ground vibration and are perfectly suited to operate in urban areas or in areas sensitive to vibration(such as near to railways, vulnerable piping systems, under structures, and historic buildings.) Thanks to own resonance-free starting and stopping , our VM vibratory hammers can be suspended from a telescopic crane, a major advantage when you have to deal with a lack of working space or you have to execute your project speedily. In addition, the ability to adjust both the moment and frequency makes a VM vibrator the perfect hammer for different soil types and different profiles.
Design and R&D
• Requirement Analysis
Based on market research and customer needs, clarify the performance requirements of hydraulic vibratory hammers, such as working parameters and applicable working conditions.
• Scheme Design
Professional engineers design the overall structure of the product, including the layout and connection methods of various parts such as the hydraulic system, vibration system, and transmission system.
• Simulation and Verification
Use software such as computer-aided design (CAD) and finite element analysis (FEA) to simulate and analyze the design scheme, and optimize the structural design.
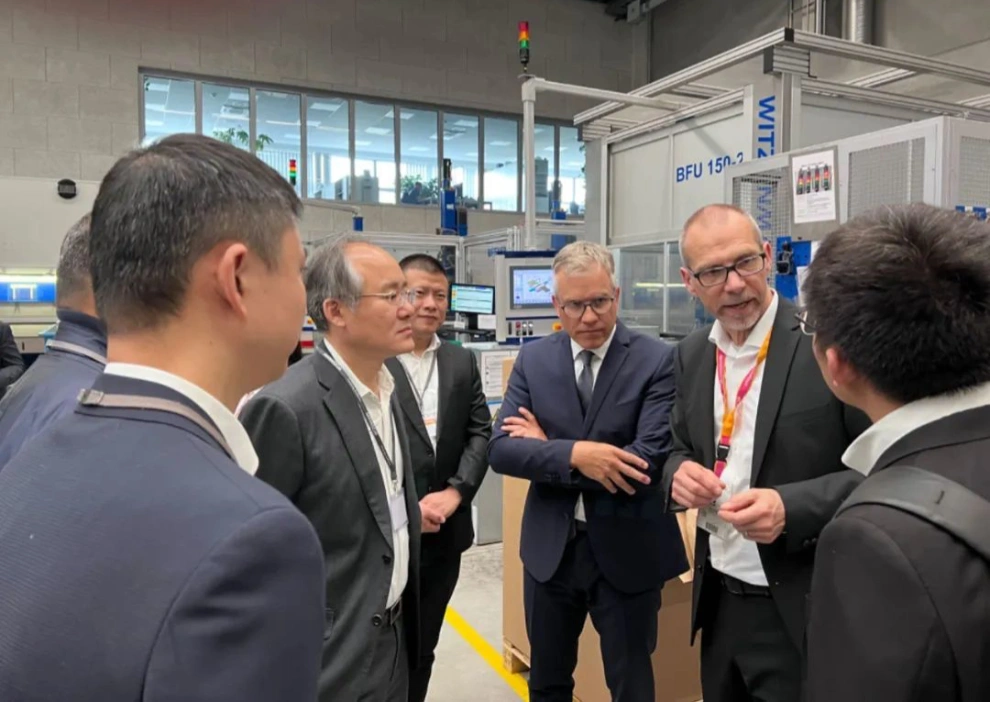
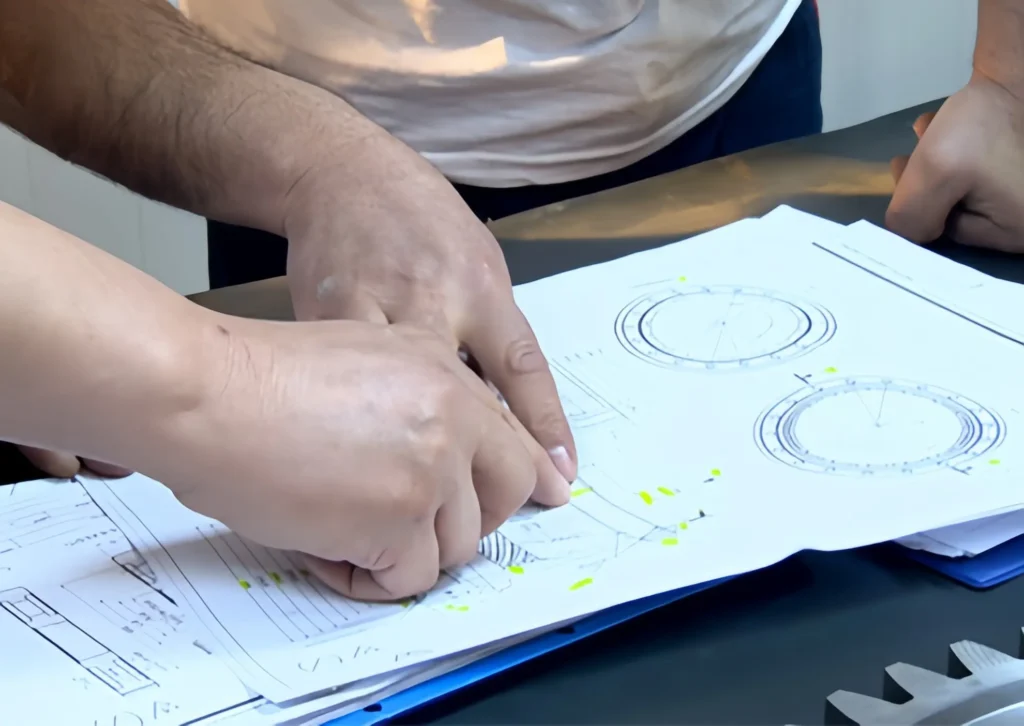
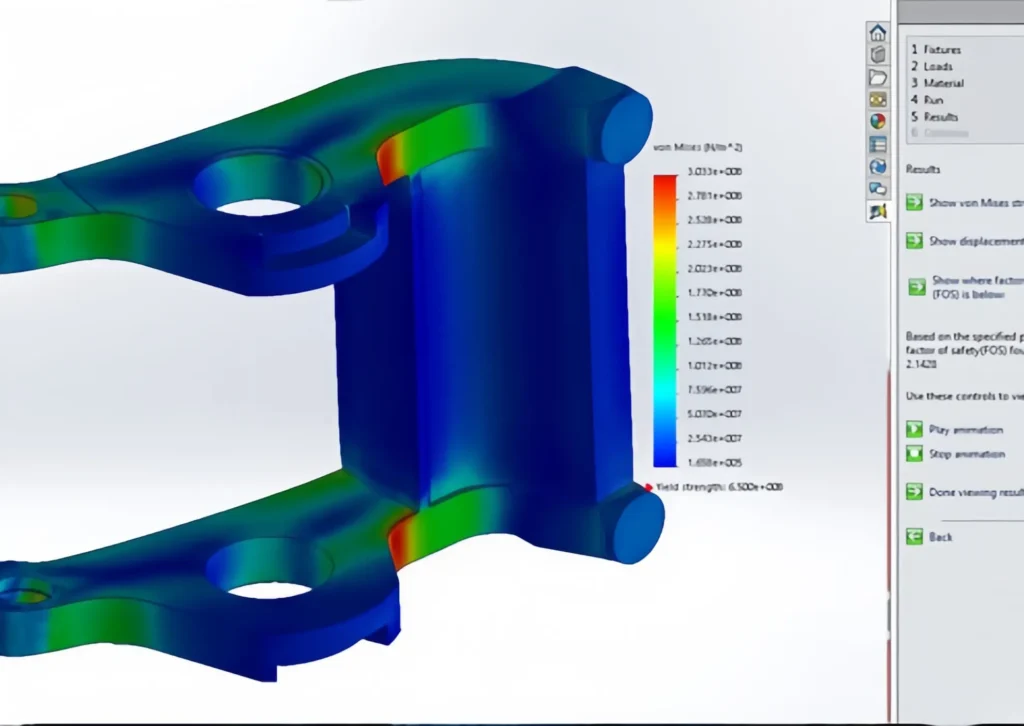
Raw Material Procurement and Inspection
• Raw Material Procurement
Purchase high-quality raw materials such as steel, castings, hydraulic components, and electrical components according to the design requirements.
• Quality Inspection
Conduct strict quality inspections on the purchased raw materials, including chemical composition analysis, mechanical property testing, dimensional accuracy measurement, etc.
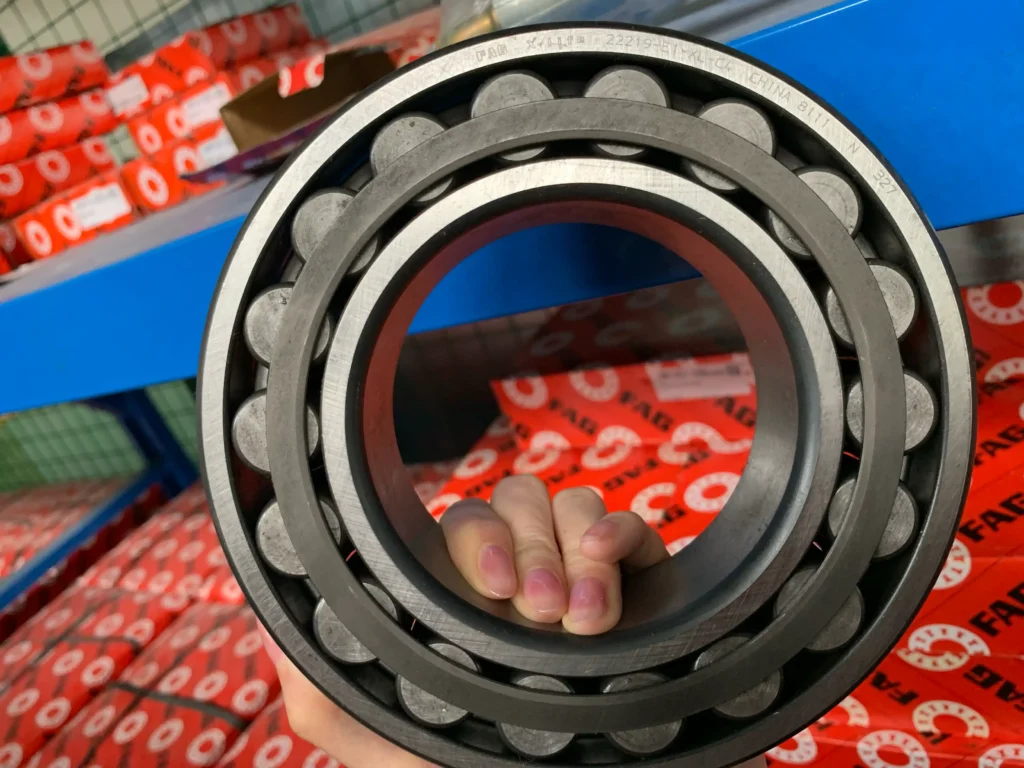
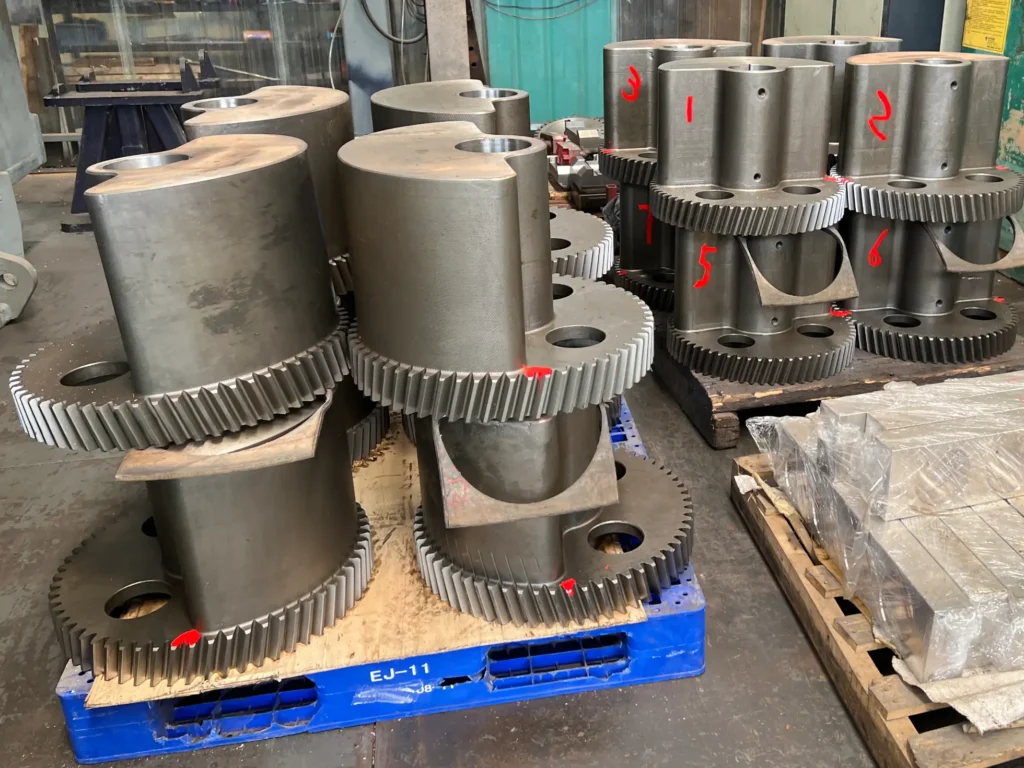
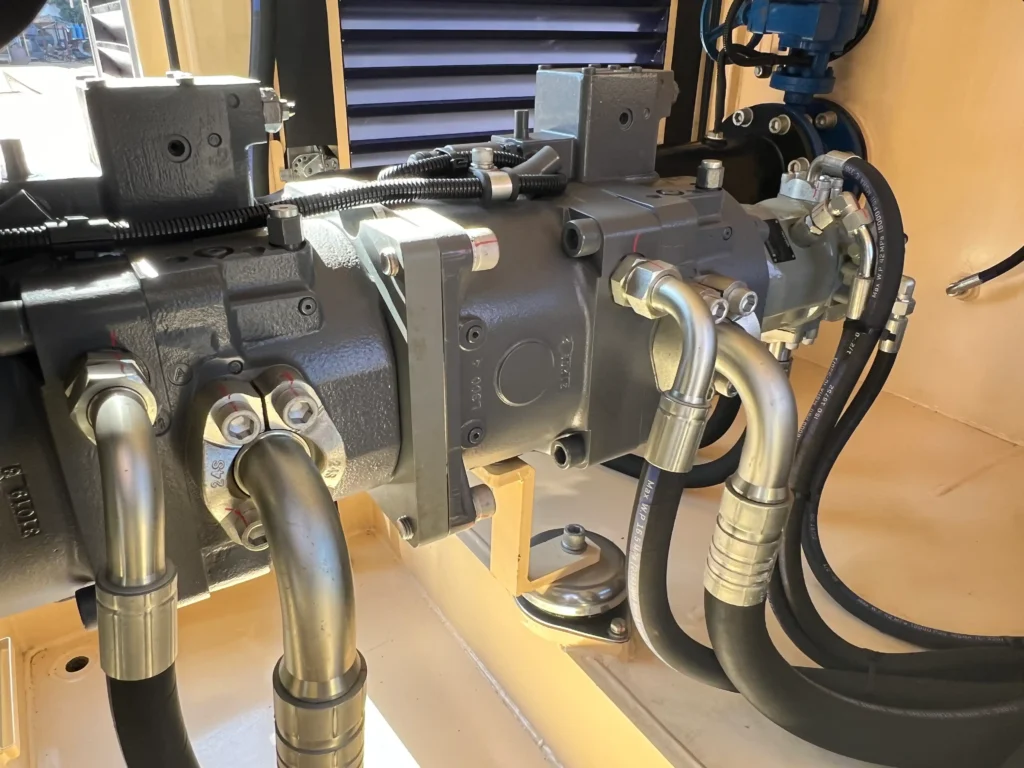
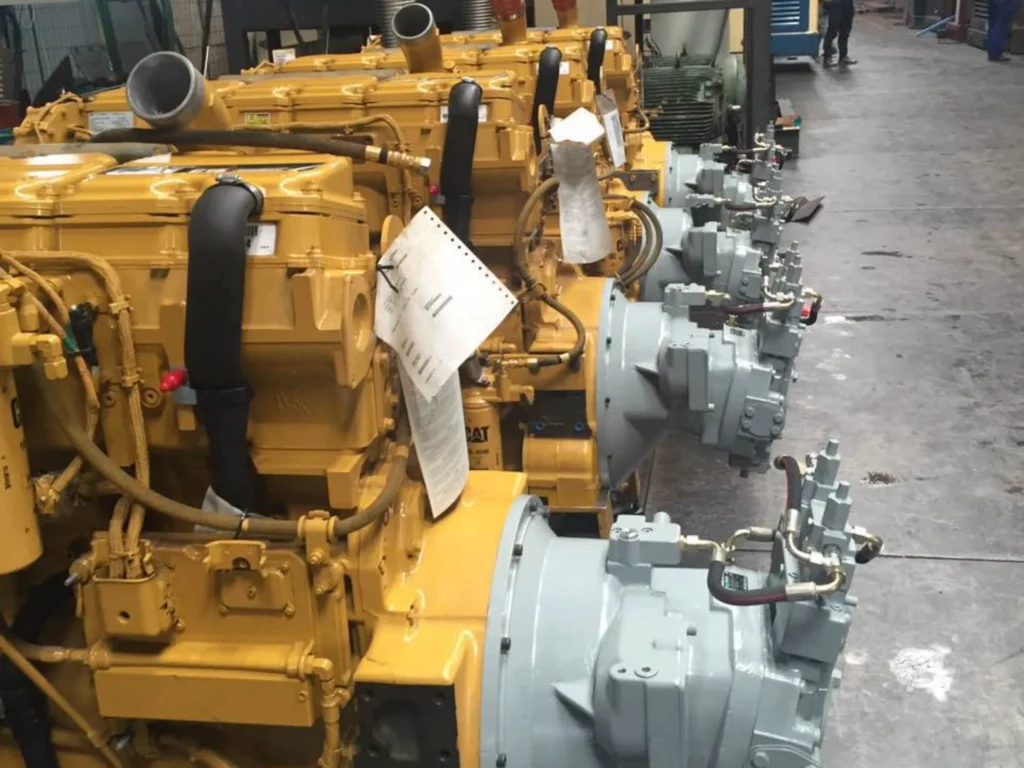
Component Processing and Manufacturing
• Machining
Use CNC lathes, milling machines, drilling machines and other equipment to perform cutting processing on metal components to ensure dimensional accuracy and surface quality.
• Heat Treatment
Perform heat treatment processes such as quenching and tempering on key components to improve the hardness, strength and wear resistance of the components.
• Surface Treatment
Perform surface treatments such as electroplating and spraying on components to improve the corrosion resistance and appearance quality of the components.

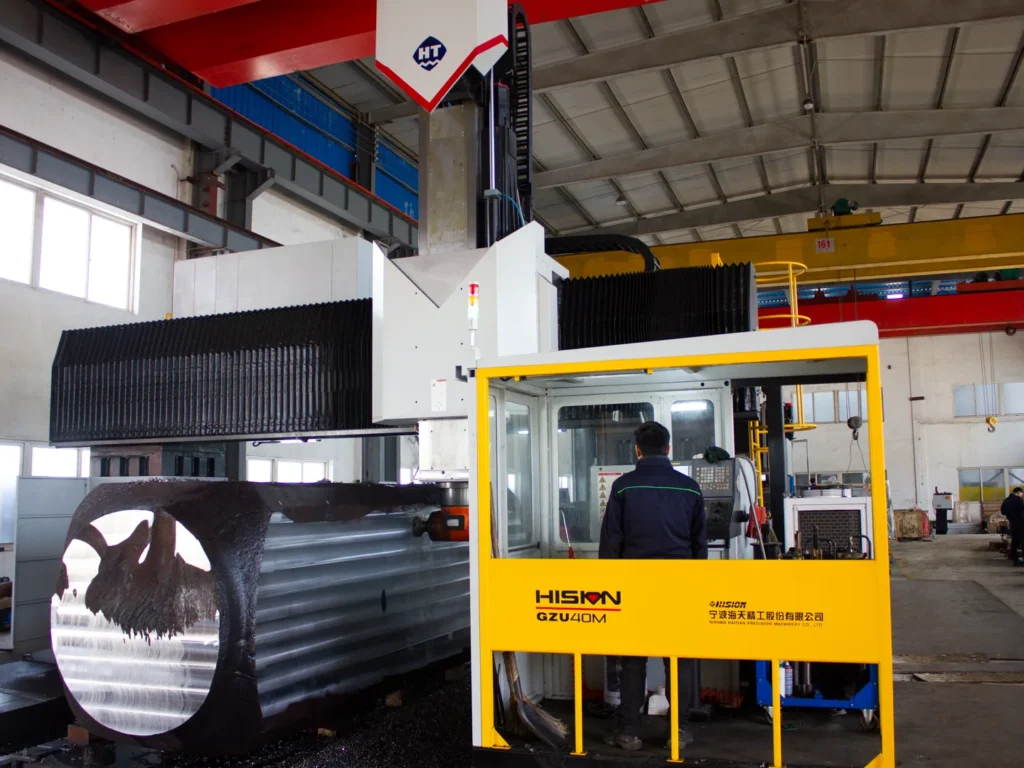

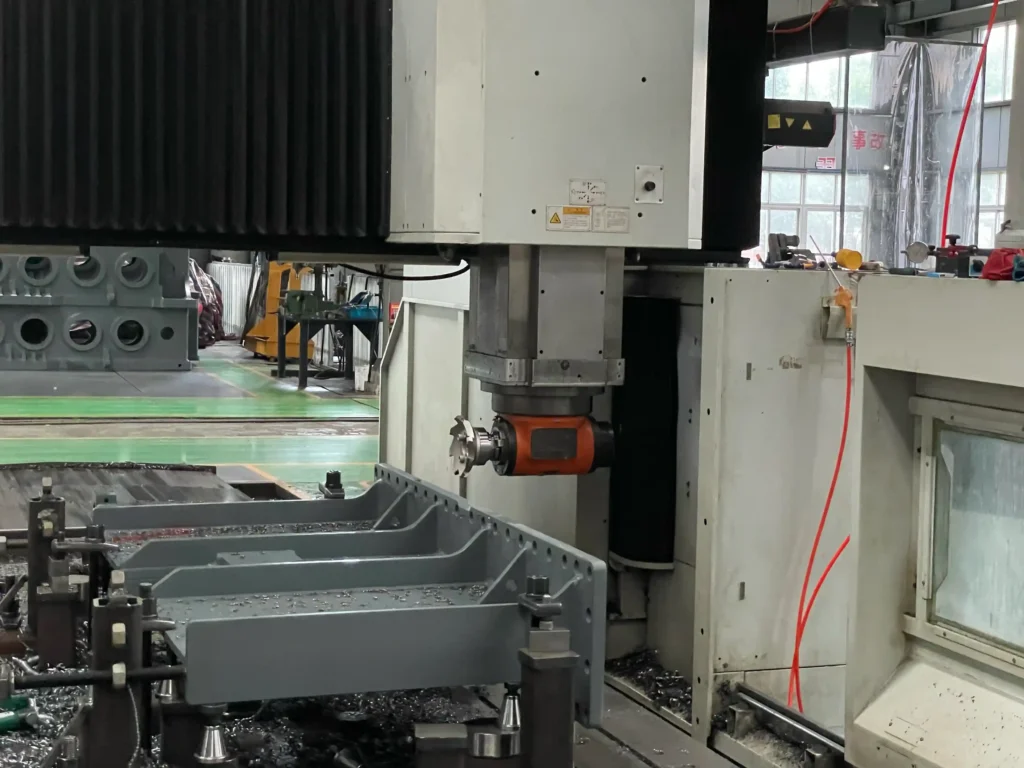
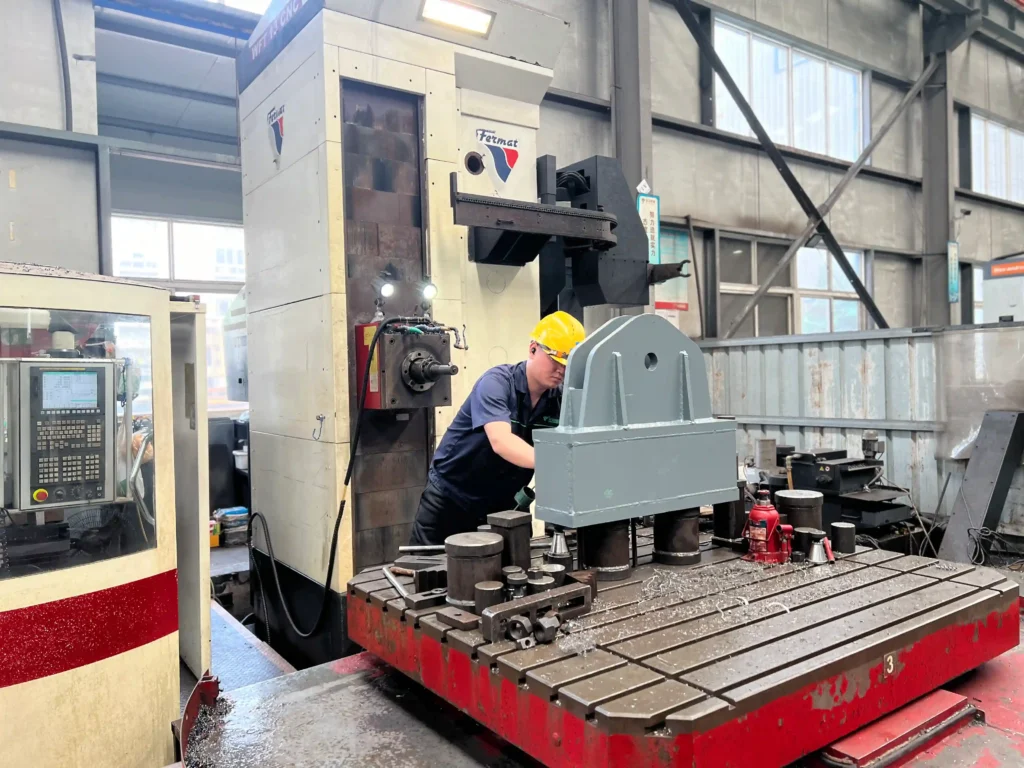
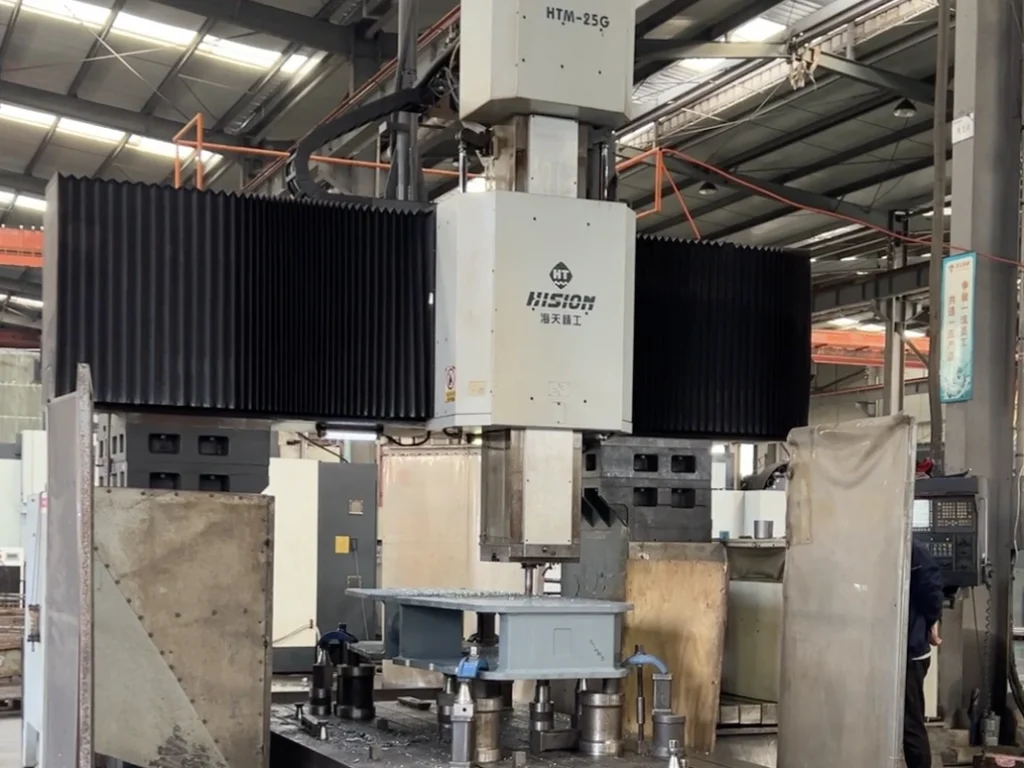
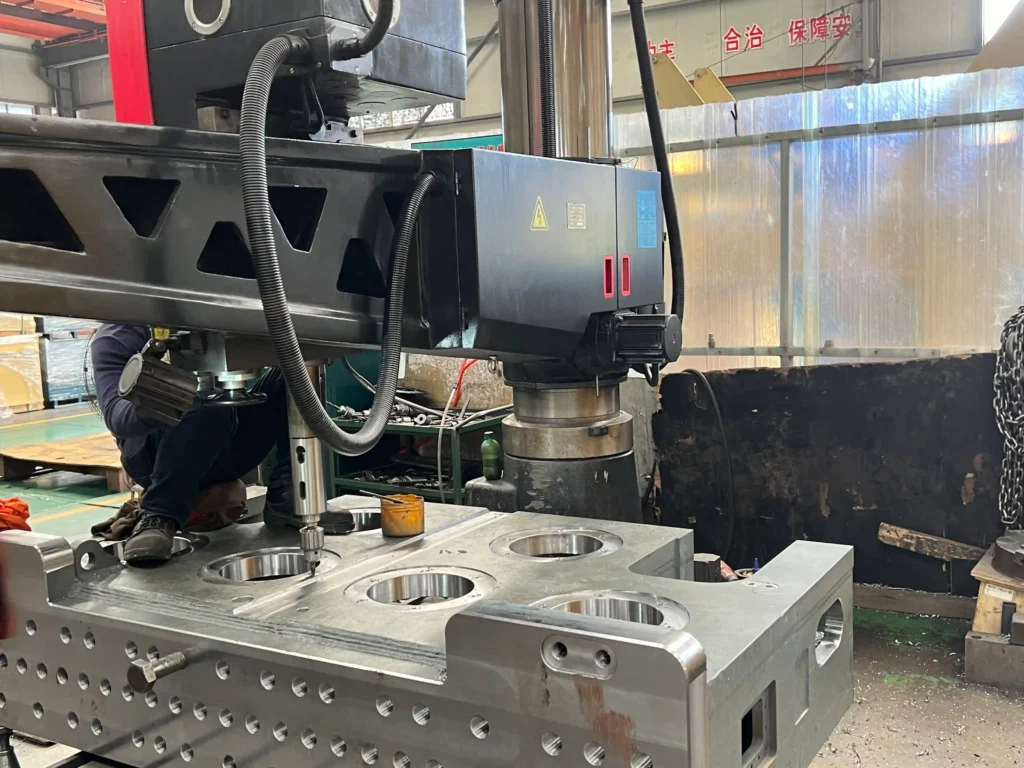
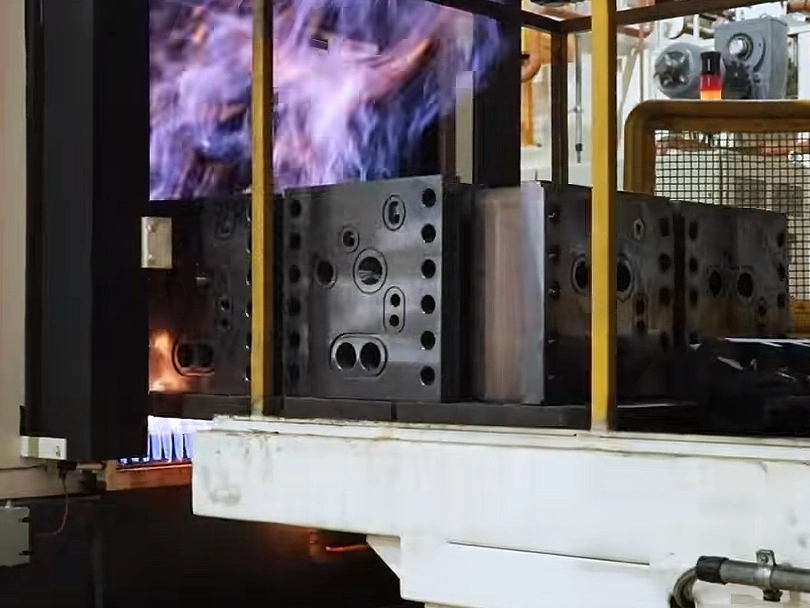
Assembly and Commissioning
• Component Assembly
Assemble the processed components according to the assembly drawing to form various components of the hydraulic vibratory hammer, such as the hydraulic power unit, vibrator, fixture, etc.
• Final Assembly and Commissioning
Assemble all components as a whole, connect hydraulic pipelines, electrical circuits, etc., and then conduct commissioning.
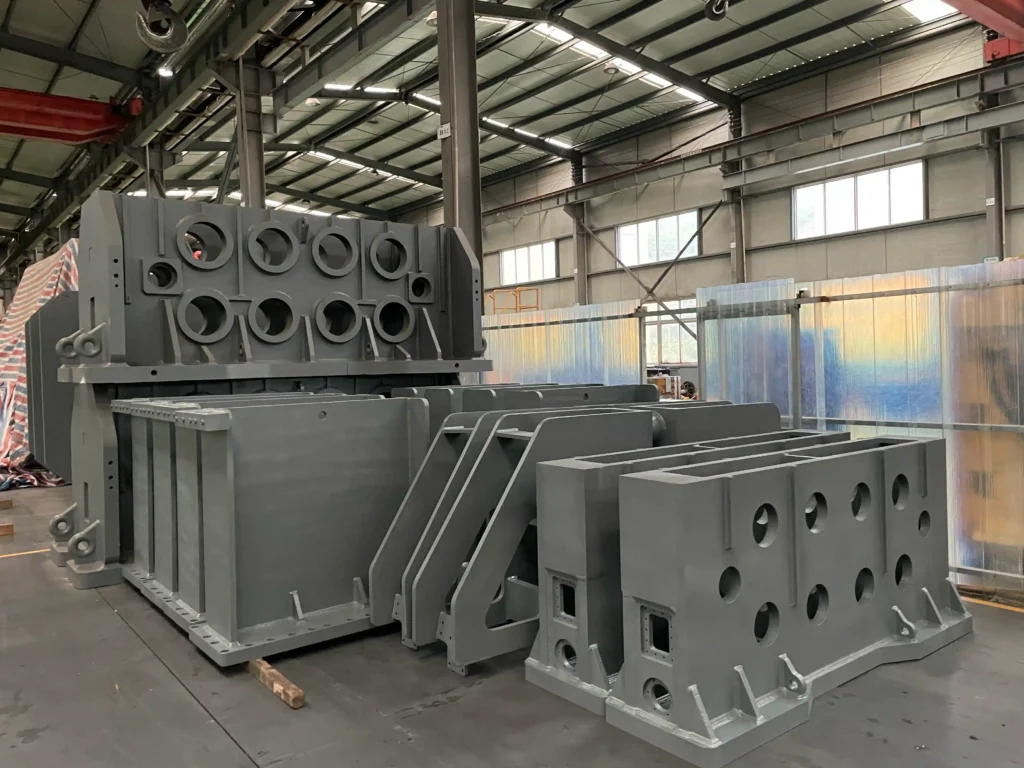
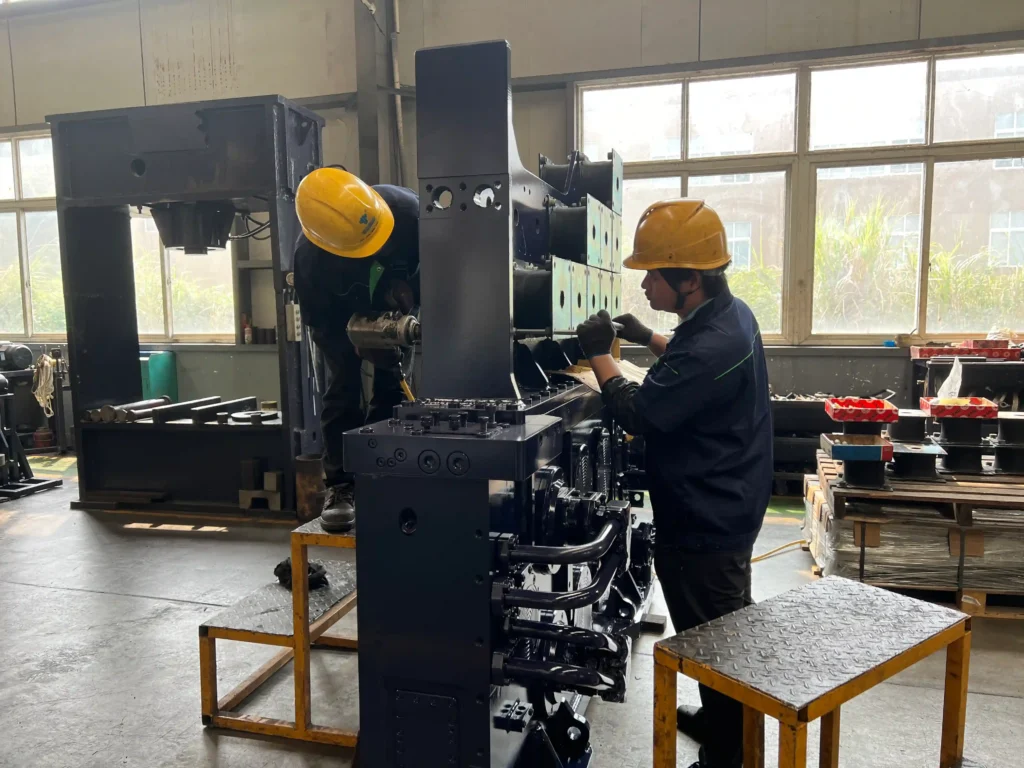
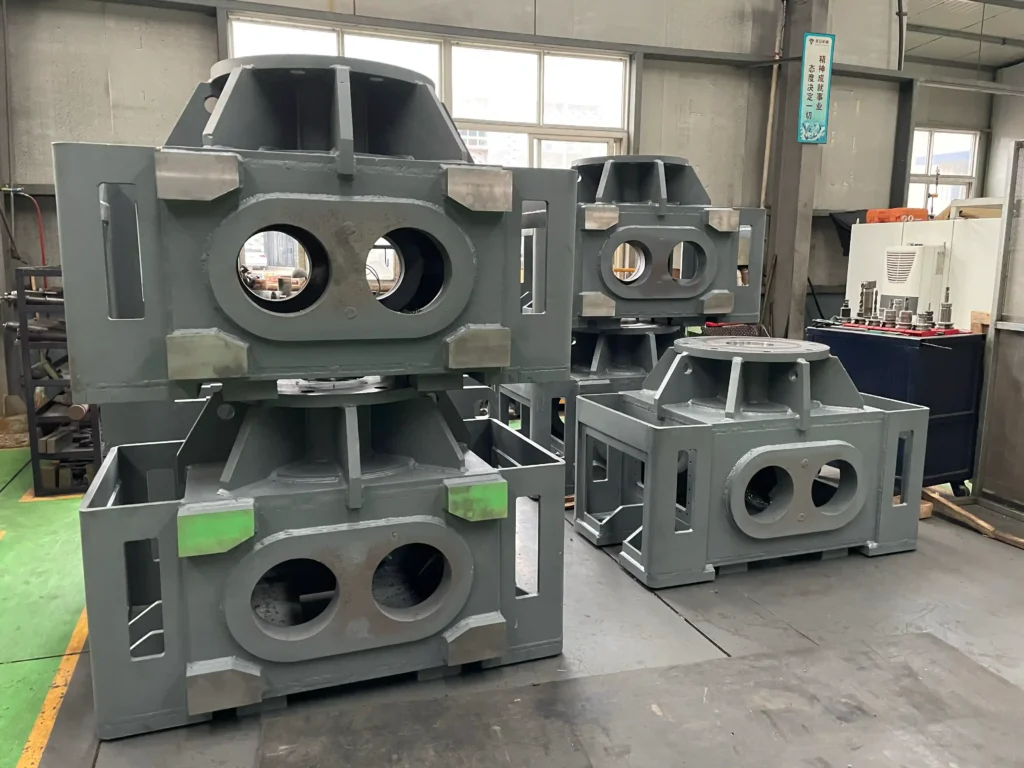
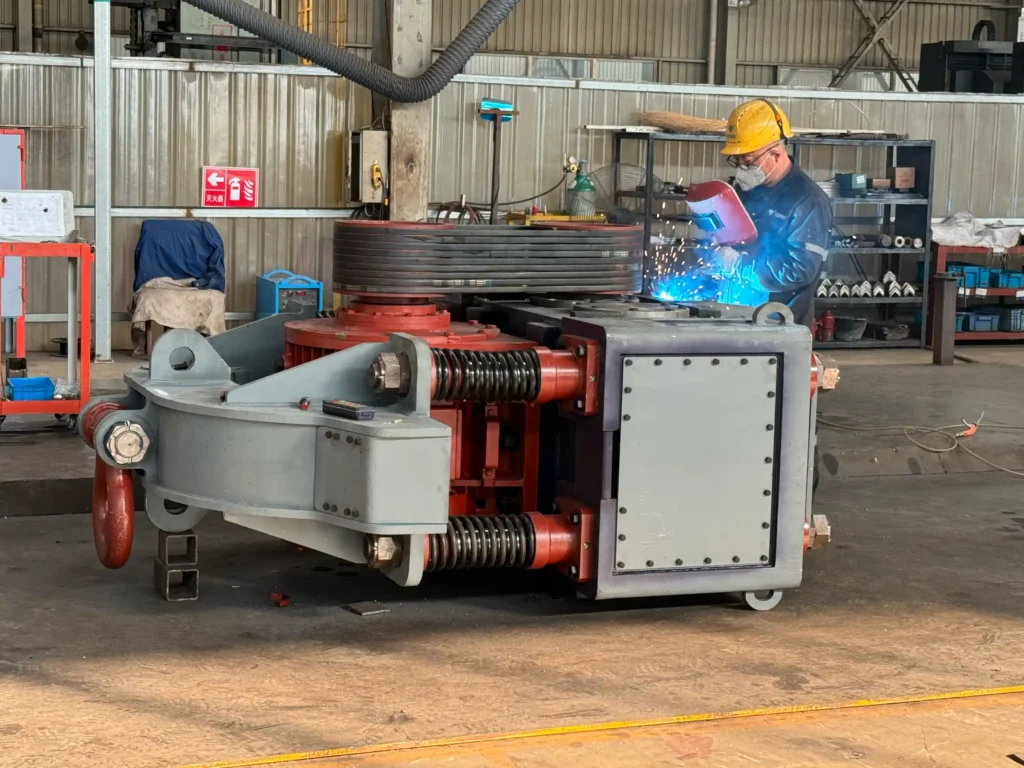
Quality Inspection and Testing
• Appearance Inspection
Inspect the appearance of the hydraulic vibratory hammer to ensure that there are no obvious defects on the surface, the paint is uniform, and the markings are clear.
• Performance Testing
Conduct comprehensive performance tests on the hydraulic vibratory hammer, including testing parameters such as vibration frequency, amplitude, exciting force, and hydraulic system pressure.
• Reliability Test
Conduct reliability tests on the hydraulic vibratory hammer, and simulate actual working conditions for long-term operation tests.
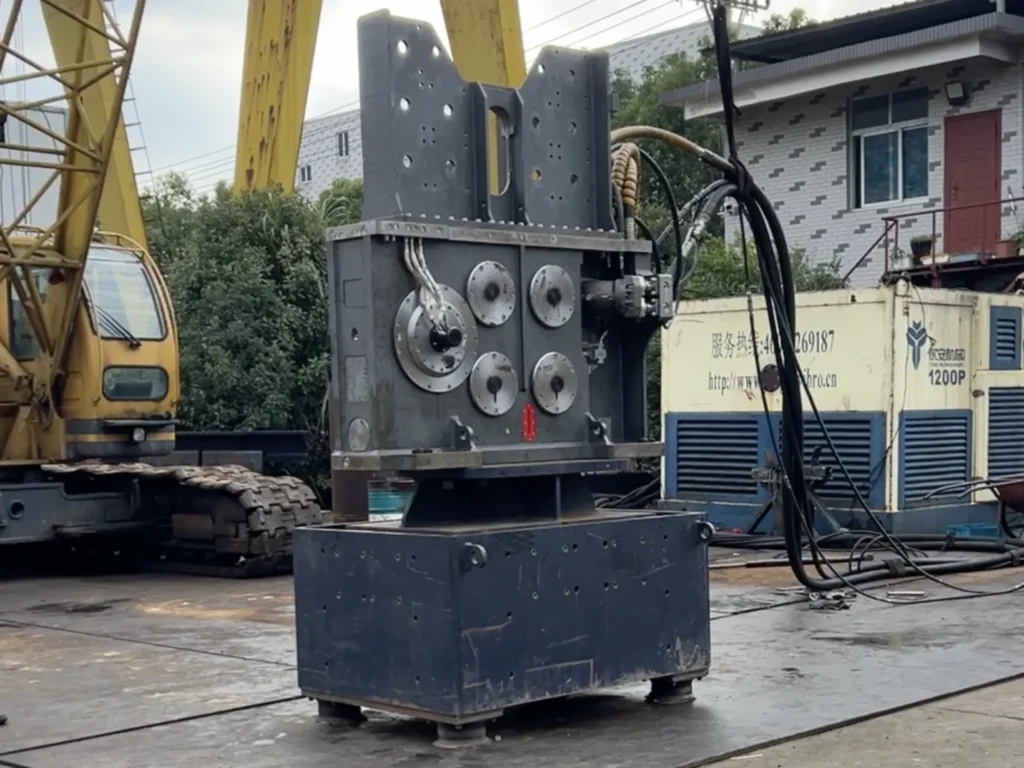
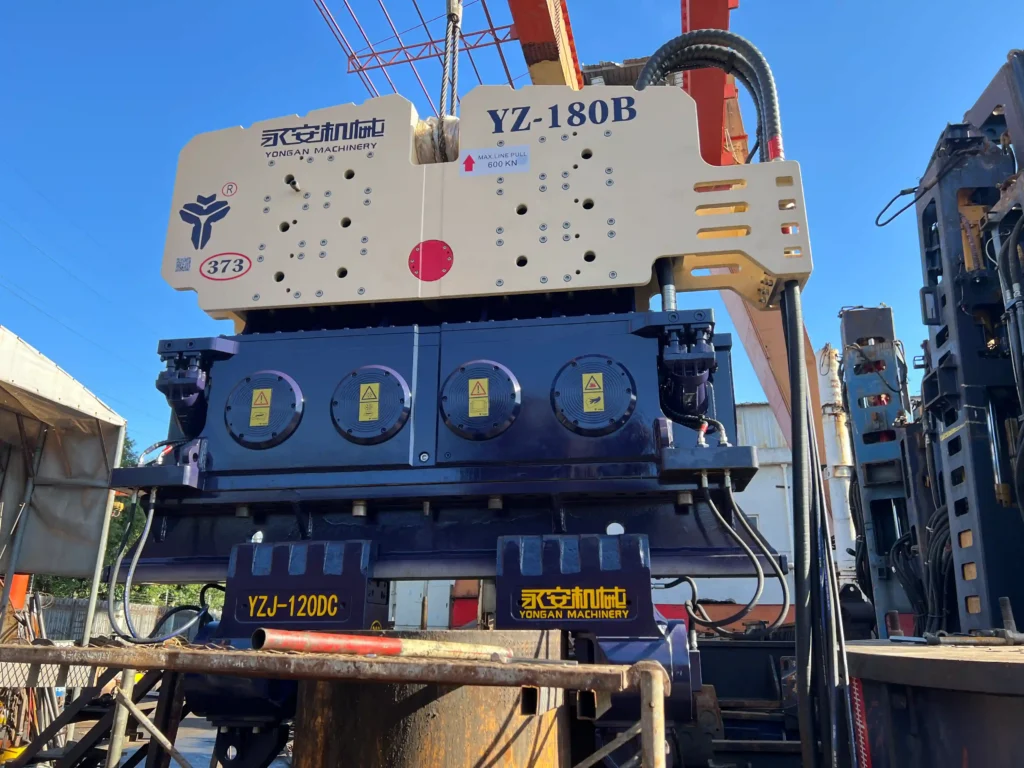
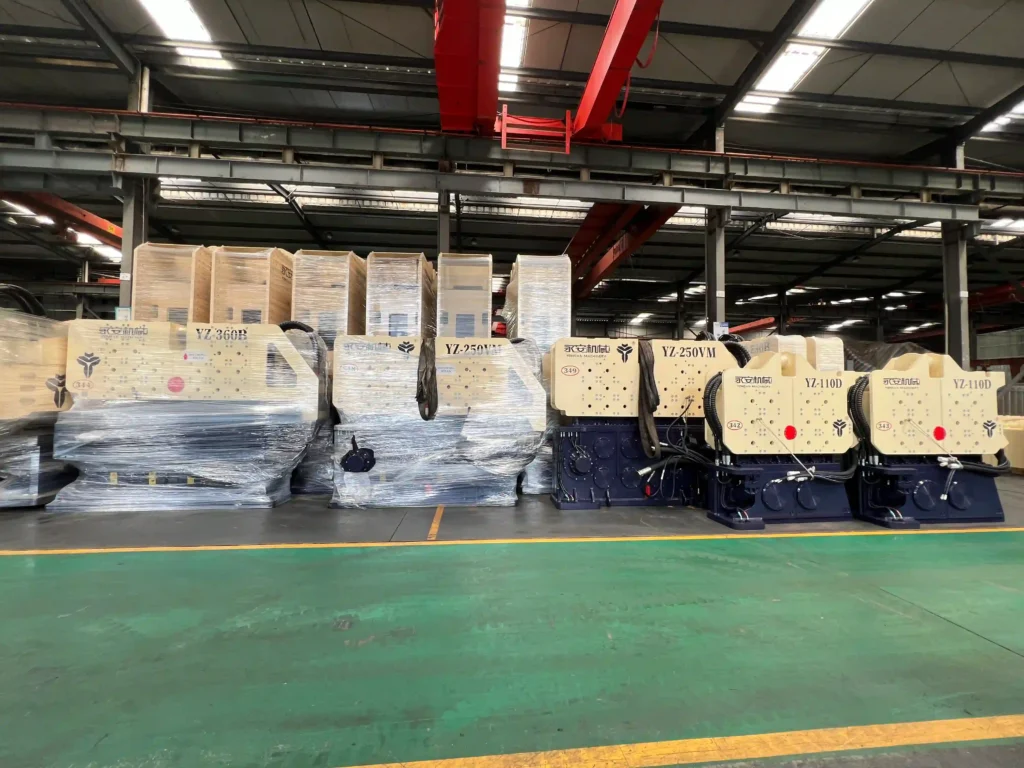
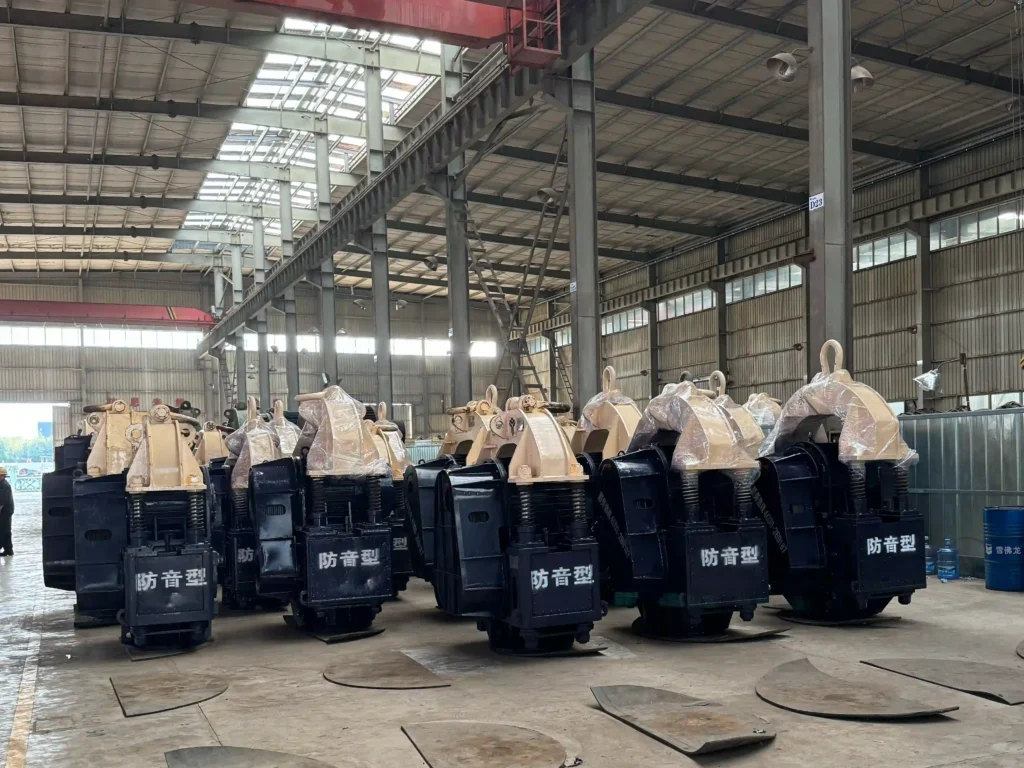